Paulig and its Poco Loco brand invest in climate-friendly food production. Paulig's high red-and-white Poco Loco warehouse in Roeselare, Belgium makes the most of their state-of-the-art technology. It is also a landmark that has decreased the number of annual truck deliveries by 25,000 simply by existing.
There are no queues of trucks circling around the Poco Loco's production facility in Roeselare, Belgium. The reason for the decreased truck traffic is a new innovative warehousing solution. It has decreased the Tex-Mex food company’s truck deliveries by up to 25,000 trips a year. In carbon dioxide emissions, this means an annual cut of a whopping 365 tonnes.
This means that tortilla chips, wraps, tacos, sauces and dips have burdened the atmosphere with significantly less carbon dioxide emissions than before when they reach the shop shelf.
A bridge spanning one hundred metres has been built between the production facility and the warehouse. The raw materials are transported along the bridge via automatic transport lines from the warehouse to the production facility, and the ready products are taken back to the warehouse along the same route.
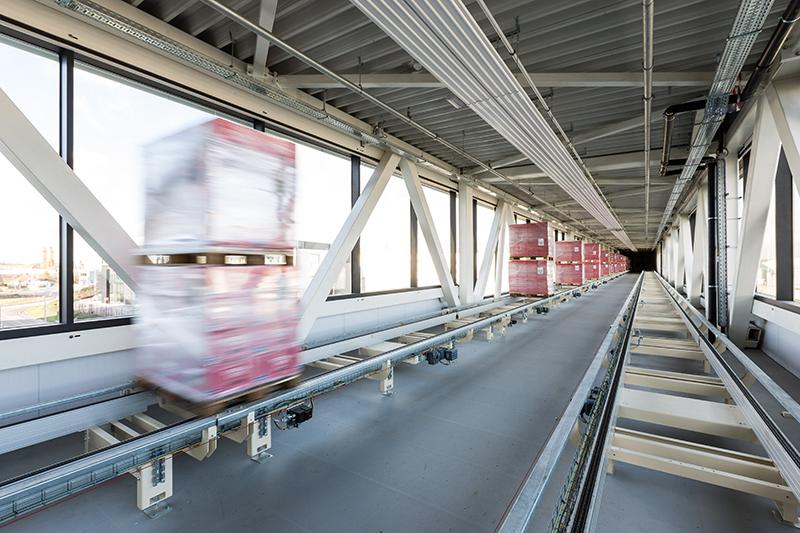
The high red-and-white warehouse is a recognisable landmark that can be seen far from along the Roeselare Port highway E403. The area of the new automated warehouse is 10,000 square metres, and it is a staggering 43 metres high.
We asked Rogier Verkarre, Paulig Group Logistics Director, for more details about this dazzling warehouse innovation and his work.
What is a typical working day like for you?
“I arrive at the office at 8 a.m. and drink a cup of coffee. After that, every day is unique, I don’t have a typical day at work. Generally, I spend about half of my time at work meeting people – helping, coaching, managing and discussing the further development of the logistics operations. The rest of the time I spend working with the Supply Chain management team and working on special projects. In addition, I travel quite often to meet the rest of the teams – approximately twice a month.”
“If I have time, I circle around the warehouses and factory areas and talk to people. This helps me understand what is happening on the shop floor and how the operations could be developed.”
What was your first reaction when you saw the new high red-and-white warehouse solution?
“We wanted the architect to be creative – we didn’t need another grey cube. Our purpose was to get more visibility. We wanted to raise people’s curiosity and discussion. Seeing the sketches for the new warehouse blew me away. Poco Loco in Spanish means “a little crazy”. I think the stunning design of the warehouse couldn’t fit the company any better.”
How unique a solution is the Paulig's Poco Loco warehouse?
“Automated, high warehouses are generally becoming more common in companies of developed industries. So the concept and technology as such aren’t new. However, the high level of automation and the technology used to manage the warehouse make the solution very unique.”
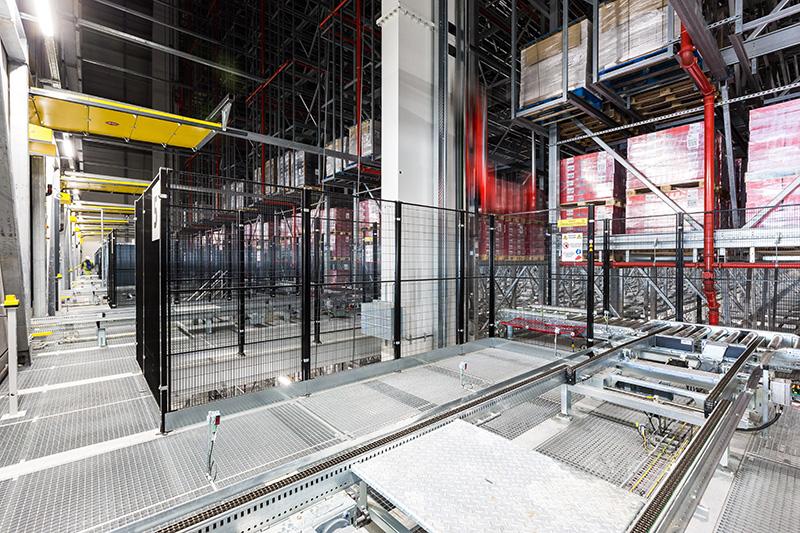
What is the most innovative aspect about the entire project?
“Most of the warehouses are operated with a special warehouse management system (WMS). Often, the difficulty with WMSs is the inconsistency of data in different data systems. To avoid these kinds of data issues, we developed a tailored WMS solution as part of our Microsoft Dynamic AX environment. This way, we could build one version of the truth. Now, the sales, planning and warehouse workers are all looking at the same numbers. We are very proud of the solution, and so we presented it at a very significant industry event in Dublin in 2017.”
How would you describe the role of IT as an enabler of the project?
“This kind of an installation would not be possible without a great IT system and tools. All the objectives, functionalities and selected algorithms must seamlessly work together. This can only be achieved with robust and modern IT tools.”
How would you describe the financial effects of the warehouse on the business operations?
“This was a very comprehensive investment. We no longer need a third party to carry out inventories. In addition, the investment will pay itself back in 8 years, thanks to the high degree of automation. It has had a positive effect on our EBIT right from the first year onwards.”
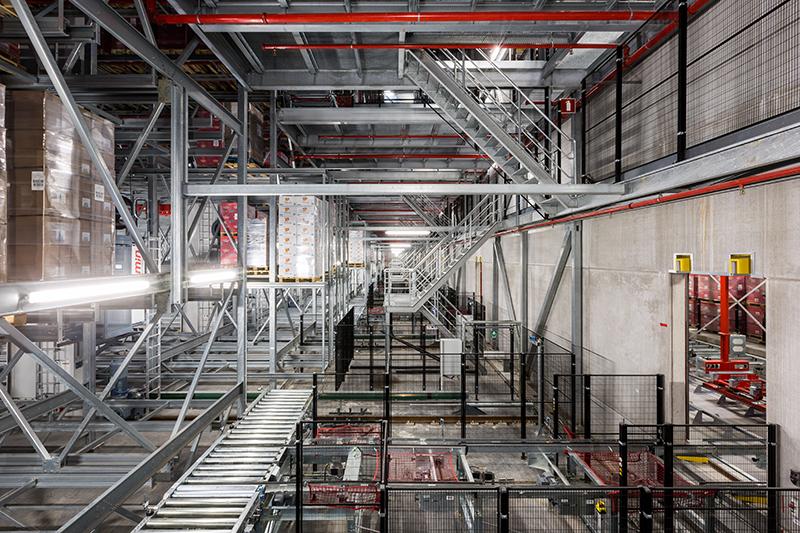
The warehouse innovation has clearly decreased your truck traffic. How would you describe the climate effects of the new solution?
“The warehouse has direct contact with production, eliminating the need for truck traffic between the production and warehouse. According to our calculations, this decreases the number of annual truck trips by 25,000, which corresponds to 365 tonnes lower carbon dioxide emissions. In the future, we can also get a windmill close by the warehouse, which would make the warehouse completely free of carbon dioxide.”
What personally inspires you most about the Paulig's Poco Loco warehousing innovation? Why?
“Optimising material flows is a constant challenge in the supply chain. By avoiding unnecessary product handling, we cut losses and make our operations more agile. In the design we have strongly focused in developing these things.”
What was the most challenging aspect of the process?
“The magnitude of the project and number of involved parties made it quite complex.”
What is the next innovative step in the future?
“We are currently working with packaging development and developing material flows. We want to develop our production into a direction that decreases warehousing products and buffering. In addition, we want to convert the warehouse into a central location, as a sort of a hub that connects and delivers products to all of our customers in Central Europe.”
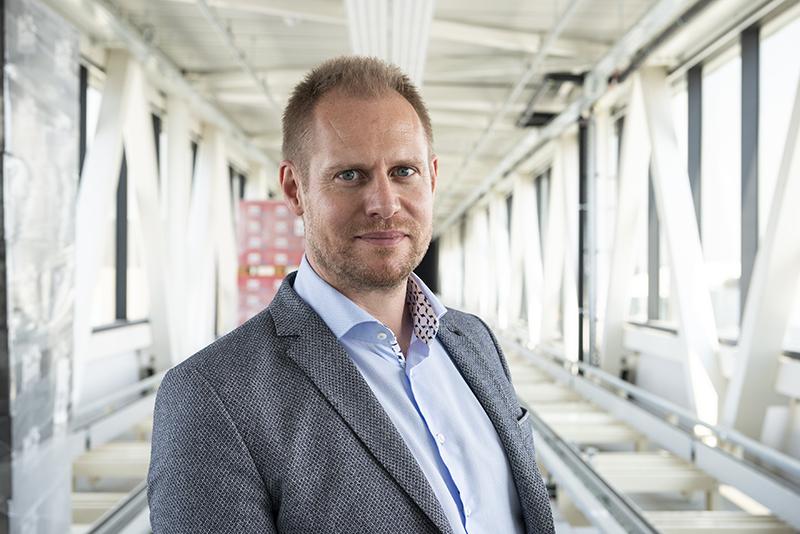
Rogier Verkarre
Career: During his career, Rogier Verkarre has worked in several managerial positions related to production, logistics and IT. He has worked with Poco Loco brand for 10 years. Before Poco Loco, he was employed by the European Latexco company for 8 years. Verkarre started his career as a process engineer at a Belgian factory. He has lived in Spain and the United States, where he was involved in setting up new factories, among other things.
Hobbies: “When I have spare time, I try to be a good father to my daughters who are 6, 9 and 11 years old. I also enjoy the small and larger renovation projects at home. I’m also practicing and teaching karate for over 25 years.”
Motto: “A goal without a plan is just a wish.”